印刷インキのトラブル、原因と対策
Printing ink problems, causes and solutions
印刷インキのトラブルとその原因、対策について、印刷版式ごとに紹介しています。
印刷インキのトラブル、原因と対策 (PDF)
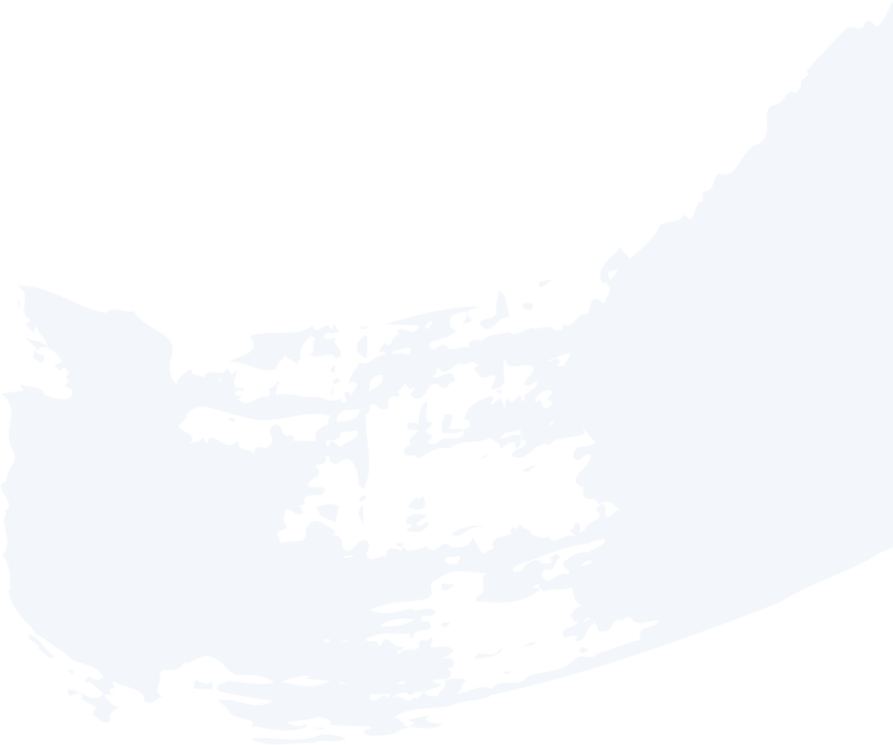
グラビア印刷
トラブル | 状態 | 原因 | 対策 |
---|---|---|---|
光沢不良 | 印刷面の光沢が極度に悪い |
|
|
濃度低下 | 濃度が低下し、初期の濃度がでない |
|
|
転移不良 | フィルムにインキがうまく移っていかない |
|
|
接着不良 | フィルムにインキが十分接着しない |
|
|
版づまり | 画線部 (特に版調部分) のインキがフィルムに転移せず印刷面がかすれる |
|
|
発泡 | 図柄の網点が部分的に消える 部分的なかすれを生ずる |
|
|
ドクターすじ | 刷込み時、非画線部に流れ方向のすじが出る |
|
|
版かぶり | 非画線部全面にうすい汚れがでる |
|
|
泳ぎ | シャドー部に不規則な流れや、見苦しいムラが出来る |
|
|
おばけ | ベタ部分が滑らかに印刷されず、斑点状になったり空白部が生じたりする |
|
|
ひげ | 画線部の周囲に糸状のはみだしを生じる |
|
|
トラッピング不良 | 多色刷の場合、1色目のインキ塗膜上に2色目以降のインキがうまくのらない |
|
|
ガイドローラー汚れ | ガイドローラーにインキが付着し、印刷面が汚れたり、すじがつく |
|
|
ブロッキング | 印刷したインキが重なったフィルム面にうつり、汚れる |
|
|
(注1) ソワリング [状態] 光沢低下、濃度低下、転移不良、版づまり [原因] 空気中の水分がインキパン中のインキに混入し、増粘、ゲル化を起こす。特に梅雨期などの多湿時に多く、インキの乾燥が早い場合に起こりやすい |
|||
(注2) ブラッシング (白化) [状態] 印刷面の光沢が極度に悪くなり、白けたような発色になる。接着も著しく低下する [原因] 空気中の湿気がインキ塗膜中に混入し、インキ塗膜の性状を破壊する |
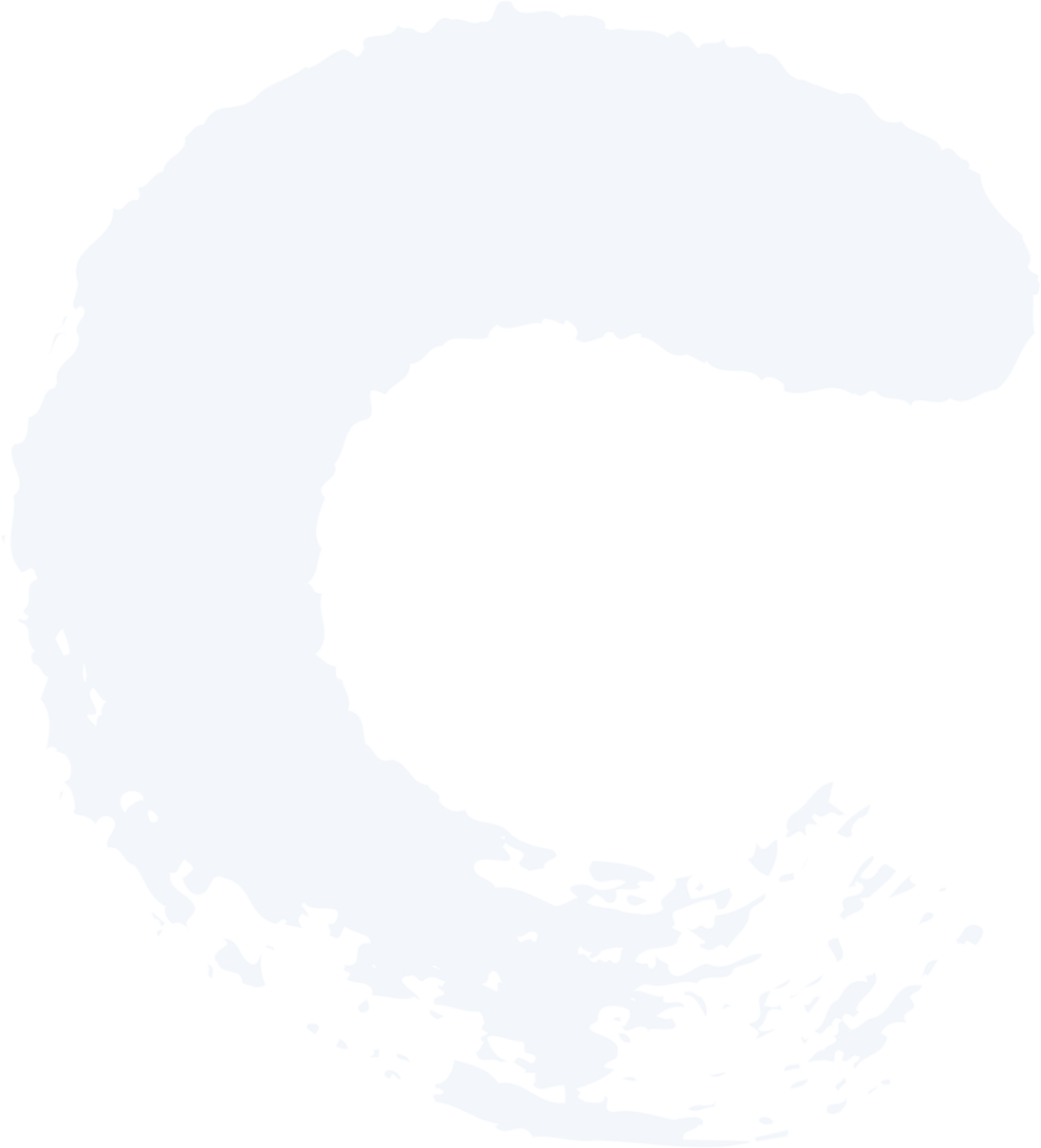
フレキソ印刷 (水性インキ)
トラブル | 状態 | 原因 | 対策 |
---|---|---|---|
色相不良 | 所定の色相が得られない |
|
|
粘度不良 | 所定の粘度が得られない |
|
|
乾燥不良 | 印刷物の乾燥不良 |
|
|
マージナルゾーン | 図柄がふちどったようになる |
|
|
版づまり | 細い図柄や文字がつぶれる |
|
|
転移不良 | インキが紙によく移っていかない |
|
|
トラッピング不良 | 重ね刷りがうまくできない |
|
|
泡立ち | インキが泡立つ |
|
|
ピンホール | 印刷面にピンホールを生じる |
|
|
版の摩耗 | 版の摩耗が激しい |
|
|
ゲル化 | インキがゲル化する |
|
|
耐性不良 | 印刷物の耐性が不十分である |
|
|
(注1) ゴムの老化による弾性損失、硬化など (注2) 循環して5分程度経過した後に測定する (注3) 添加量はインキの0.2%程度とする (注4) できるだけ低い粘度にする (注5) 特に、ベタ印刷には35~45°のものを使用する (注6) 絞りローラーのゴムの老化、弾性消失、アニロックス・ローラーの目詰り、摩耗など (注7) 1色目の印圧はできるだけ軽くすること (注8) 粘度差を3秒以上にする (注9) 添加量はインキの0.2%程度とする |
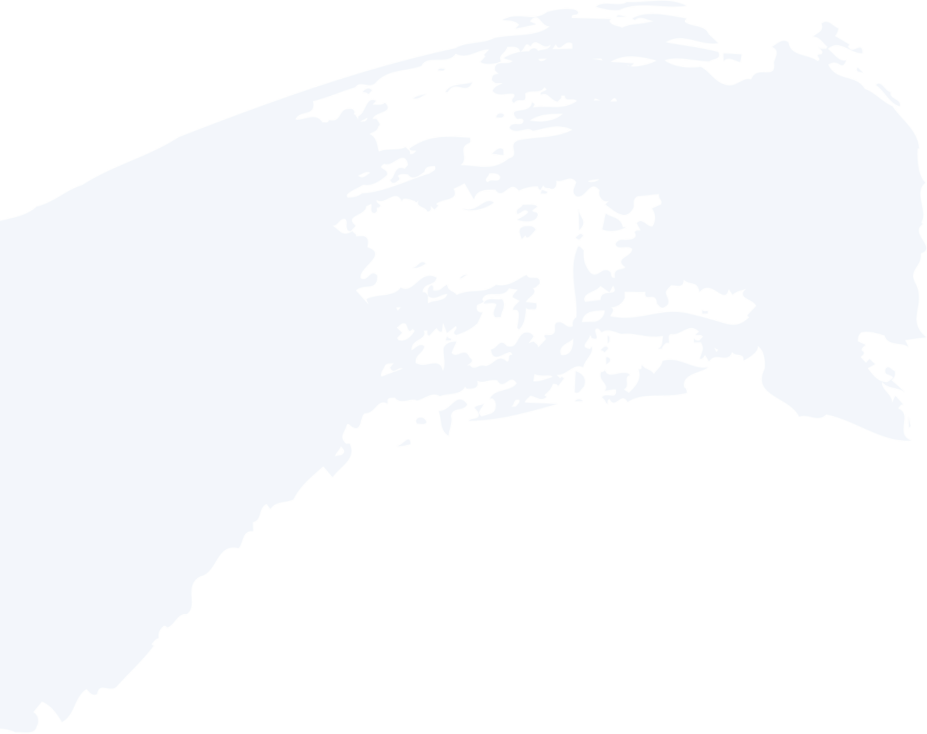
枚葉印刷 (枚葉・オフ輪共通)
トラブル | 状態 | 原因 | 対策 |
---|---|---|---|
壺あがり | インキ壺からインキが呼び出しローラーに転移しない 印刷物が段々と淡くなる |
|
|
パイリング (版残り、ブラン残り) | 印刷中にインキの転移が十分でなく、ローラー版、ブランケットにインキがたまる そのために印刷面のベタの着きが均一でなくなる 網点の部分がムラになる 画線が太る |
|
|
ピッキング (紙むけ) | 紙がむける |
|
|
チョーキング | 表面が乾いているのに、印刷面を指でこすると取れる |
|
|
トラッピング不良 (インキののりが悪い) | 多色機ウエットプリントにおけるインキの重ね刷り不良でモットリング (表面が凹凸状態) になる |
|
|
地汚れ | 版に感じている汚れ |
|
|
浮き汚れ | インキの粒子が湿し水中に浮遊して、印刷面全面に移動して汚れる |
|
|
ヒッキー | 印刷部分がところどころ白点状にぬける |
|
|
ミスチング | 印刷中にインキが練りローラーの間から霧状に飛ぶ |
|
|
ローラーストリッピング (ローラーはげ) | インキングローラーがインキを受け付けなくなり、表面があらわれてくる |
|
|
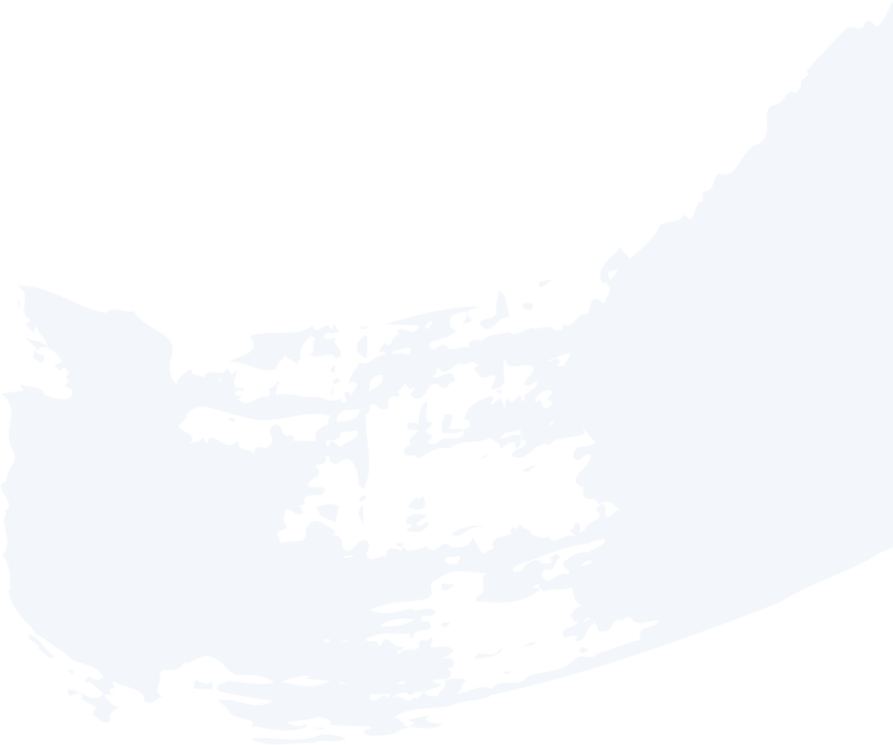
枚葉印刷
トラブル | 状態 | 原因 | 対策 |
---|---|---|---|
裏うつり (ブロッキング、ステッキング) | 印刷したインキがセット乾燥する段階で上紙の裏面につき、汚れる (その程度により左の名称で呼ばれる) |
|
|
乾燥不良 | いつまでもインキがベタつく (アフタータック) |
|
|
グロスゴースト | 印刷物の裏面での追い刷り時に現われる光沢の差 |
|
|
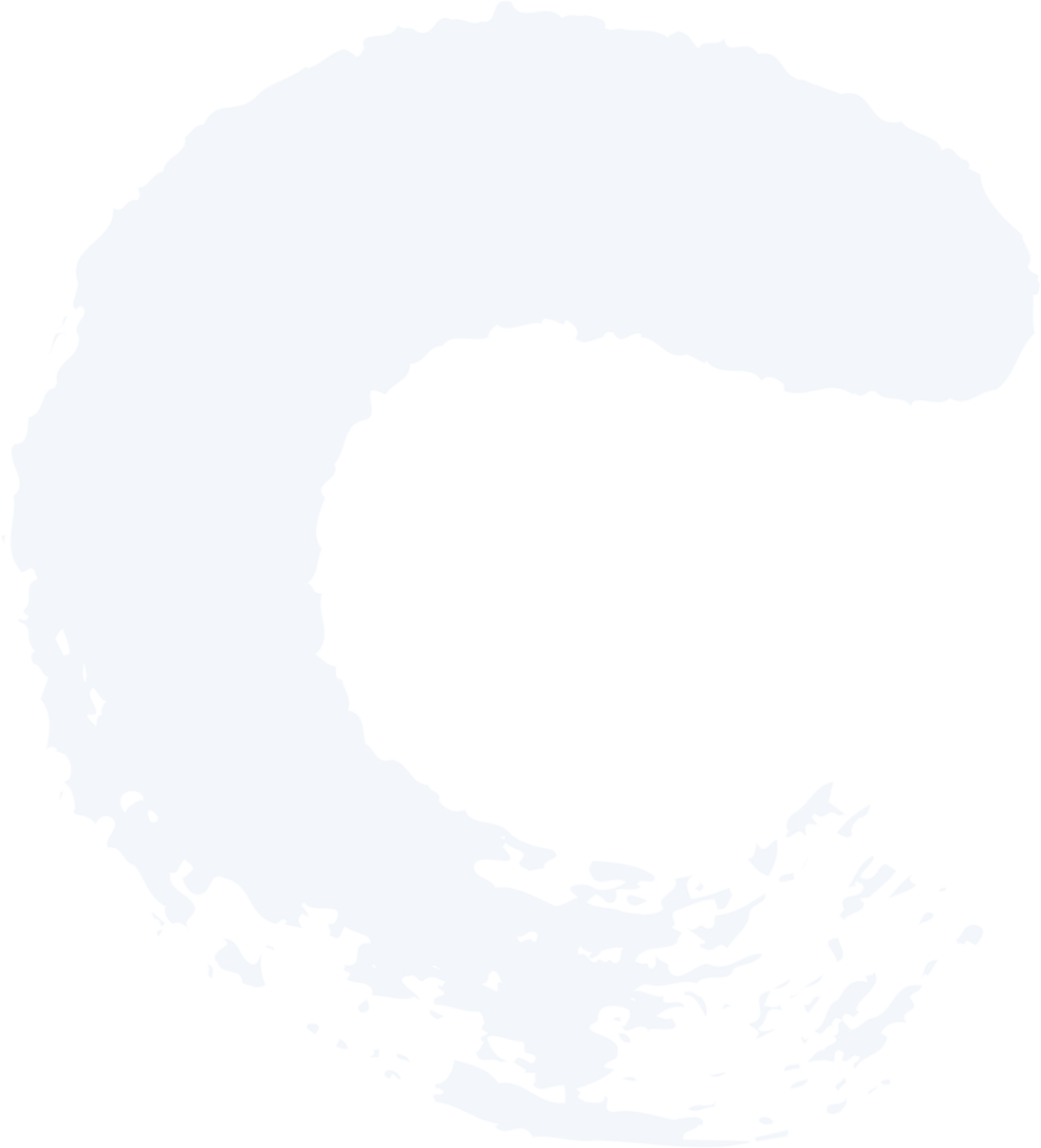
オフ輪印刷
トラブル | 状態 | 原因 | 対策 |
---|---|---|---|
ブリスター | 用紙がドライヤを通過する時に生じる火ぶくれのこと 絵柄のベタ部に発生しやすく、丸みを帯び、輪郭がはっきりしているのが特徴で、紙の両面から確認できる |
|
|
デラミネーション | 走行中の紙が、ブランケットに取られてバタつき、見当不良・ダブリが発生する |
|
|
クーリング縦じわ | 刷本に発生する縦じわで、全面に認められる |
|
|
火じわ | 刷本の画線部と非画線部の収縮差により縦じわが生じる 紙の表裏の収縮差により凹凸状のしわが発生する |
|
|
乾燥不良 | ガイドローラー汚れ、ターンバー汚れ、フォーマー汚れ |
|
|
ガイドローラー/ターンバー/フォーマー汚れ | 印刷された走行紙が、オーブン通過後、ガイドローラー・ターンバーを通ってフォーマーで折られるが、ガイドローラーなどにインキが取られ、走行紙方向に擦れ傷が紙面に汚れとなって現われる |
|
|
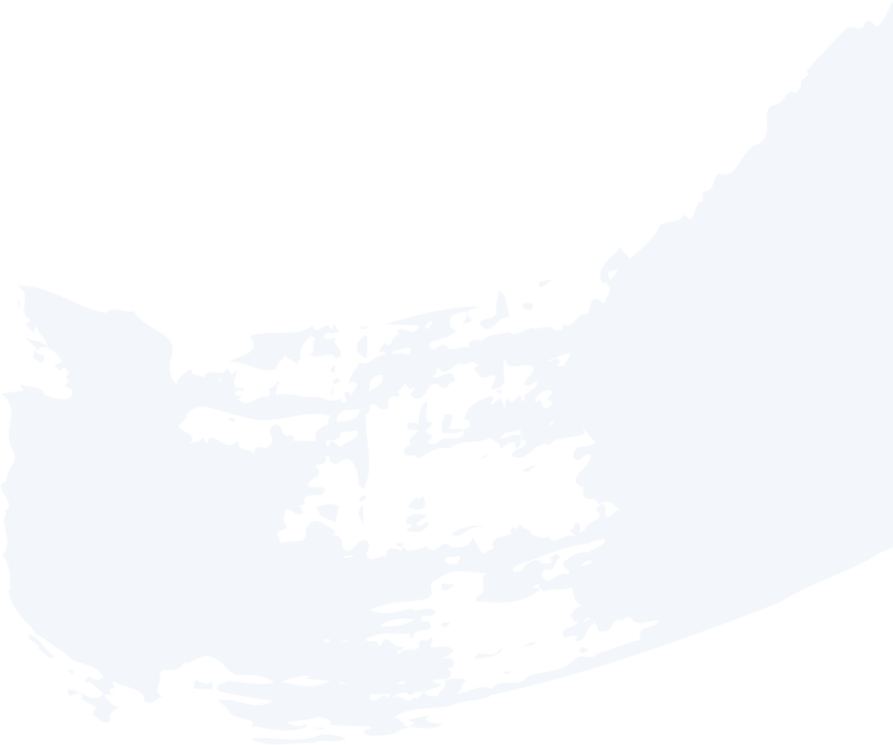
グラビア印刷
トラブル | 状態 | 原因 | 対策 |
---|---|---|---|
光沢不良 | 印刷面の光沢が極度に悪い |
|
|
濃度低下 | 濃度が低下し、初期の濃度がでない |
|
|
転移不良 | フィルムにインキがうまく移っていかない |
|
|
接着不良 | フィルムにインキが十分接着しない |
|
|
版づまり | 画線部 (特に版調部分) のインキがフィルムに転移せず印刷面がかすれる |
|
|
発泡 | 図柄の網点が部分的に消える 部分的なかすれを生ずる |
|
|
ドクターすじ | 刷込み時、非画線部に流れ方向のすじが出る |
|
|
版かぶり | 非画線部全面にうすい汚れがでる |
|
|
泳ぎ | シャドー部に不規則な流れや、見苦しいムラが出来る |
|
|
おばけ | ベタ部分が滑らかに印刷されず、斑点状になったり空白部が生じたりする |
|
|
ひげ | 画線部の周囲に糸状のはみだしを生じる |
|
|
トラッピング不良 | 多色刷の場合、1色目のインキ塗膜上に2色目以降のインキがうまくのらない |
|
|
ガイドローラー汚れ | ガイドローラーにインキが付着し、印刷面が汚れたり、すじがつく |
|
|
ブロッキング | 印刷したインキが重なったフィルム面にうつり、汚れる |
|
|
(注1) ソワリング [状態] 光沢低下、濃度低下、転移不良、版づまり [原因] 空気中の水分がインキパン中のインキに混入し、増粘、ゲル化を起こす。特に梅雨期などの多湿時に多く、インキの乾燥が早い場合に起こりやすい |
|||
(注2) ブラッシング (白化) [状態] 印刷面の光沢が極度に悪くなり、白けたような発色になる。接着も著しく低下する [原因] 空気中の湿気がインキ塗膜中に混入し、インキ塗膜の性状を破壊する |
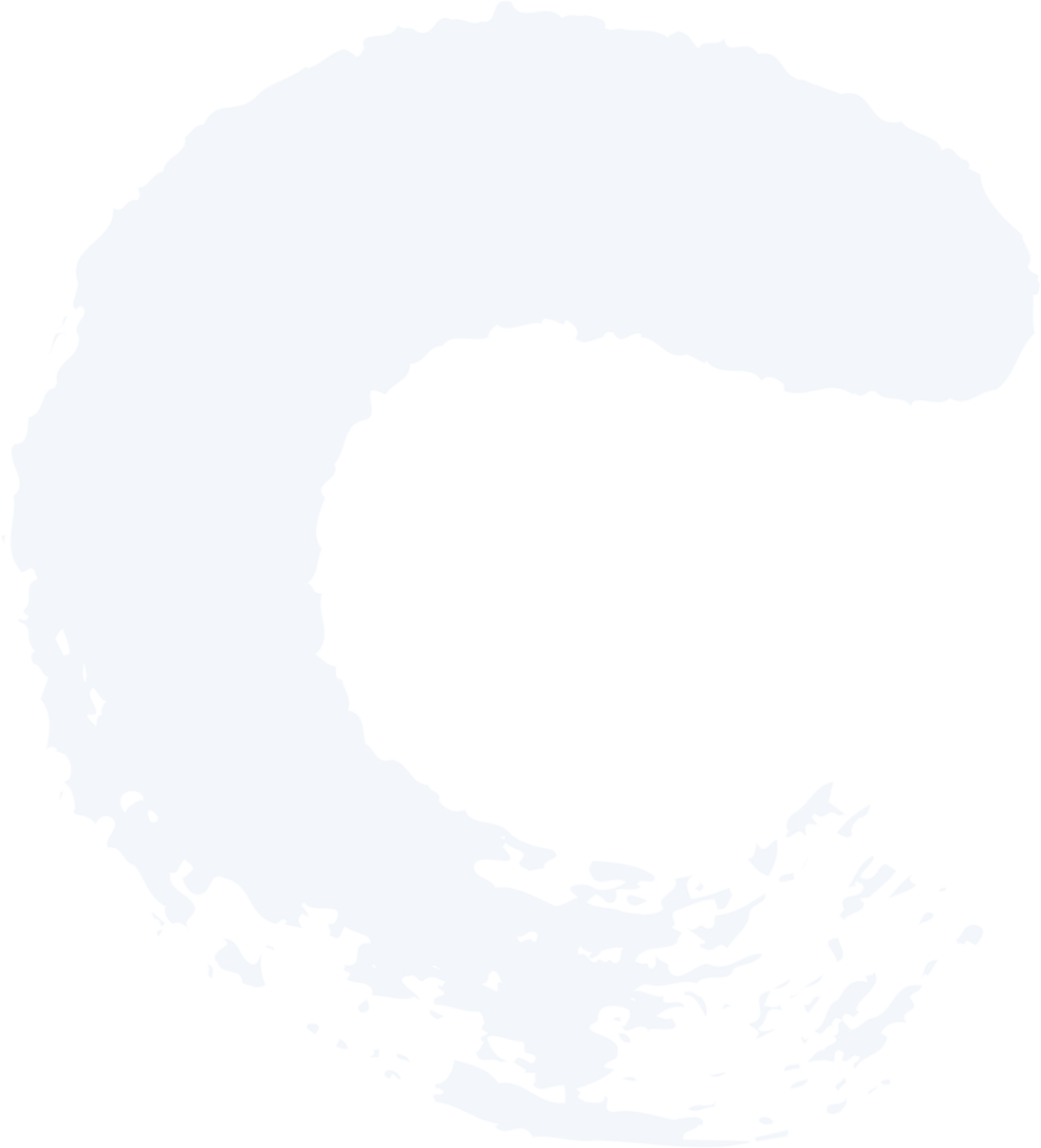
フレキソ印刷 (水性インキ)
トラブル | 状態 | 原因 | 対策 |
---|---|---|---|
色相不良 | 所定の色相が得られない |
|
|
粘度不良 | 所定の粘度が得られない |
|
|
乾燥不良 | 印刷物の乾燥不良 |
|
|
マージナルゾーン | 図柄がふちどったようになる |
|
|
版づまり | 細い図柄や文字がつぶれる |
|
|
転移不良 | インキが紙によく移っていかない |
|
|
トラッピング不良 | 重ね刷りがうまくできない |
|
|
泡立ち | インキが泡立つ |
|
|
ピンホール | 印刷面にピンホールを生じる |
|
|
版の摩耗 | 版の摩耗が激しい |
|
|
ゲル化 | インキがゲル化する |
|
|
耐性不良 | 印刷物の耐性が不十分である |
|
|
(注1) ゴムの老化による弾性損失、硬化など (注2) 循環して5分程度経過した後に測定する (注3) 添加量はインキの0.2%程度とする (注4) できるだけ低い粘度にする (注5) 特に、ベタ印刷には35~45°のものを使用する (注6) 絞りローラーのゴムの老化、弾性消失、アニロックス・ローラーの目詰り、摩耗など (注7) 1色目の印圧はできるだけ軽くすること (注8) 粘度差を3秒以上にする (注9) 添加量はインキの0.2%程度とする |
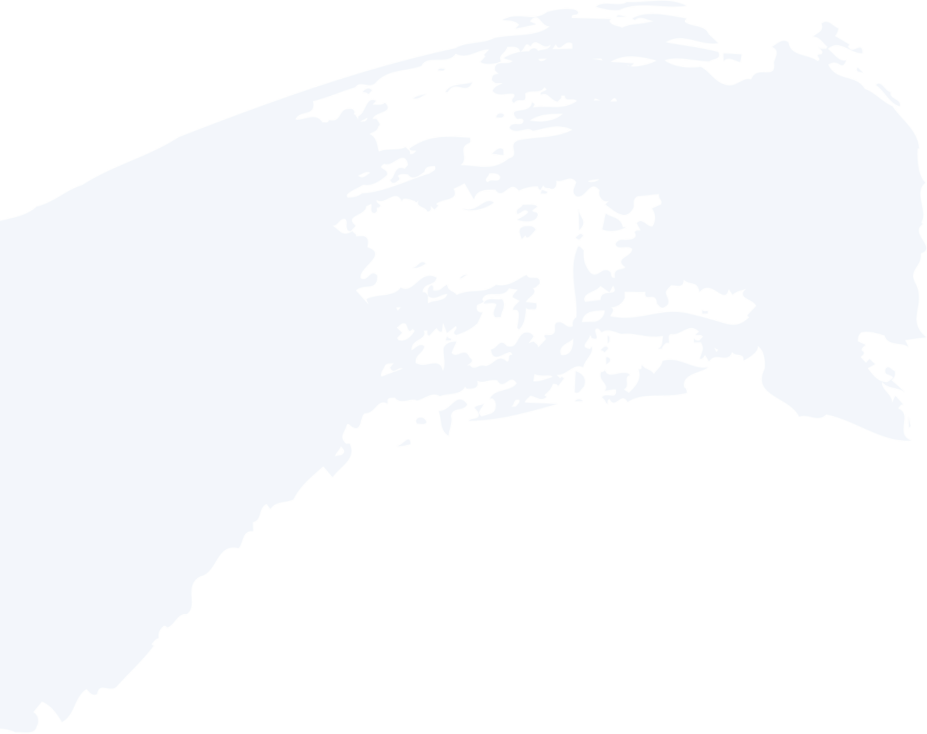
枚葉印刷 (枚葉・オフ輪共通)
トラブル | 状態 | 原因 | 対策 |
---|---|---|---|
壺あがり | インキ壺からインキが呼び出しローラーに転移しない 印刷物が段々と淡くなる |
|
|
パイリング (版残り、ブラン残り) | 印刷中にインキの転移が十分でなく、ローラー版、ブランケットにインキがたまる そのために印刷面のベタの着きが均一でなくなる 網点の部分がムラになる 画線が太る |
|
|
ピッキング (紙むけ) | 紙がむける |
|
|
チョーキング | 表面が乾いているのに、印刷面を指でこすると取れる |
|
|
トラッピング不良 (インキののりが悪い) | 多色機ウエットプリントにおけるインキの重ね刷り不良でモットリング (表面が凹凸状態) になる |
|
|
地汚れ | 版に感じている汚れ |
|
|
浮き汚れ | インキの粒子が湿し水中に浮遊して、印刷面全面に移動して汚れる |
|
|
ヒッキー | 印刷部分がところどころ白点状にぬける |
|
|
ミスチング | 印刷中にインキが練りローラーの間から霧状に飛ぶ |
|
|
ローラーストリッピング (ローラーはげ) | インキングローラーがインキを受け付けなくなり、表面があらわれてくる |
|
|
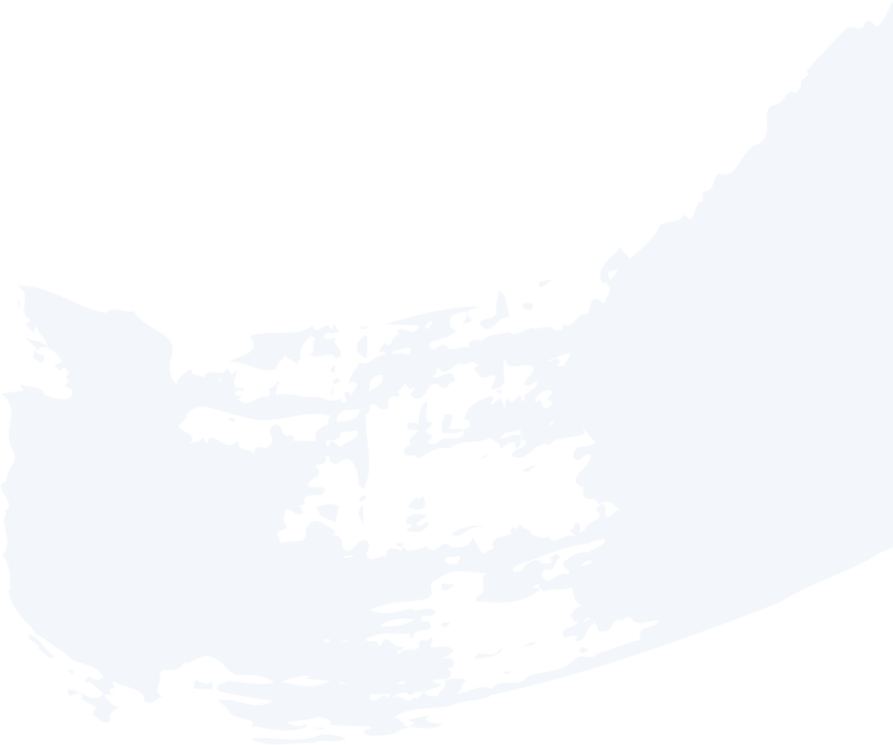
枚葉印刷
トラブル | 状態 | 原因 | 対策 |
---|---|---|---|
裏うつり (ブロッキング、ステッキング) | 印刷したインキがセット乾燥する段階で上紙の裏面につき、汚れる (その程度により左の名称で呼ばれる) |
|
|
乾燥不良 | いつまでもインキがベタつく (アフタータック) |
|
|
グロスゴースト | 印刷物の裏面での追い刷り時に現われる光沢の差 |
|
|
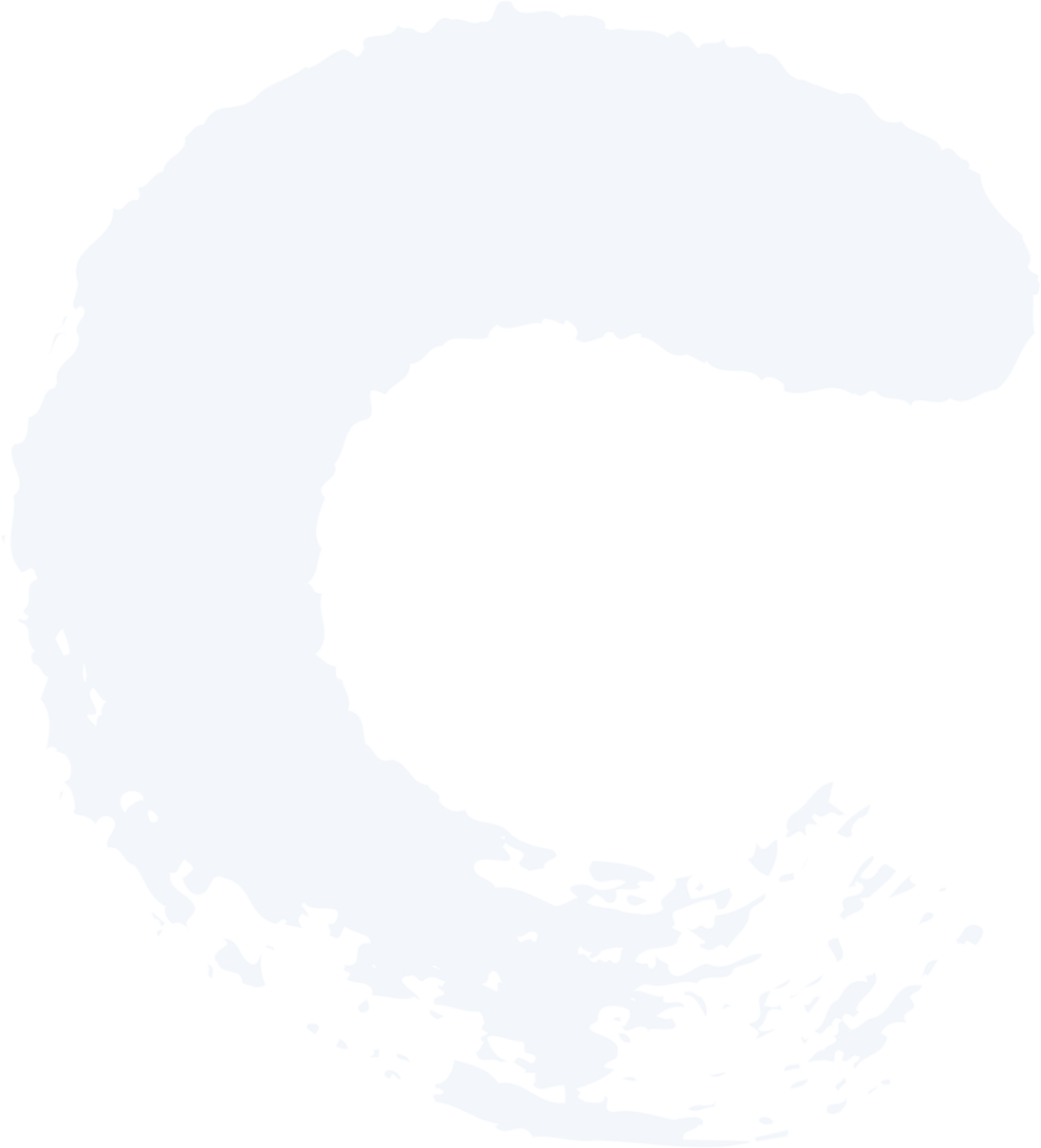
オフ輪印刷
トラブル | 状態 | 原因 | 対策 |
---|---|---|---|
ブリスター | 用紙がドライヤを通過する時に生じる火ぶくれのこと 絵柄のベタ部に発生しやすく、丸みを帯び、輪郭がはっきりしているのが特徴で、紙の両面から確認できる |
|
|
デラミネーション | 走行中の紙が、ブランケットに取られてバタつき、見当不良・ダブリが発生する |
|
|
クーリング縦じわ | 刷本に発生する縦じわで、全面に認められる |
|
|
火じわ | 刷本の画線部と非画線部の収縮差により縦じわが生じる 紙の表裏の収縮差により凹凸状のしわが発生する |
|
|
乾燥不良 | ガイドローラー汚れ、ターンバー汚れ、フォーマー汚れ |
|
|
ガイドローラー/ターンバー/フォーマー汚れ | 印刷された走行紙が、オーブン通過後、ガイドローラー・ターンバーを通ってフォーマーで折られるが、ガイドローラーなどにインキが取られ、走行紙方向に擦れ傷が紙面に汚れとなって現われる |
|
|
取り扱い製商品
製商品に関するお問い合わせ
-
グラビアパッケージ事業部
グラビアインキ
- 【大阪】
-
06-6447-5867 06-6447-5867
FAX 06-6447-5839
- 【東京】
-
04-7127-2231 04-7127-2231
FAX 04-7129-9684
-
紙・パッケージ事業部
フレキソインキ・オフセットインキ(枚葉)
- 【大阪】
-
06-6447-5866 06-6447-5866
FAX 06-6447-5839
- 【東京】
-
04-7127-2231 04-7127-2231
FAX 04-7129-9684
-
情報メディア事業部
オフセットインキ(輪転)・新聞インキ
- 【大阪】
-
06-6447-5851 06-6447-5851
FAX 06-6447-5833
- 【東京】
-
03-5689-6644 03-5689-6644
FAX 03-5689-6633