SAKATA INX aims to build “Plants that inspire stakeholders, and survive and keep winning by embodying innovative technological capabilities and strengthen its foundation” through TPM activities.
What is TPM?
TPM (Total Productive Maintenance) was first proposed by the Japan Institute of Plant Maintenance in 1971. TPM is defined as follows:
- Aim to build corporate system that pursues maximum production system efficiency (comprehensive streamlining);
- Achieve “zero accidents, zero defects, zero malfunctions” by targeting the whole lifecycle of the production system;
- Use the “go and see” method to build system in order to prevent every form of loss;
- mplement measures at every department, including production, development, sales and administration;
- Achieve “zero losses” through overlapping small group activities in which all employees from top executive to the front-line workers participate.
(Source: Japan Institute of Plant Maintenance)
Today's TPM (Total Productive Management) has now evolved to mean “production management in which all employees participate.”
Background of introduction
In order to survive in a competitive business environment and continue to develop as a company, there is a need to build a robust corporate culture that allows our company to respond flexibly to change.
For this reason, it is essential to develop and launch products that meet the needs of the market and to improve production efficiency.
In order to achieve these goals, SAKATA INX deems strengthening its production platform and fostering human resources as top priority issues. As such, we launched “TPM Activities” in April 1998.
Outline of activities
Through activities to improve personnel and facility quality by removing all losses in the production system, TPM activities make it possible to enhance corporate structure. Production system does not only mean production divisions, but also encompasses the entire business process including indirect divisions. Loss is the difference between the current state and the way that we should be. It is important to make the loss visible and make improvements, and always pursue how we should be. Moreover, we are aiming to establish the SDPS (SAKATA INX DIRECT PRODUCTION SYSTEM) as the ideal form of production system at the company.
Background of activities and results
[Part I Activities]: 1998-2004 (TPM Excellence Award received)
We developed activities with the goal to become a “Plant to Be Proud of within the Industry.”
- Priority issues are the development of attractive products, the creation of direct production lines, the development of creative people, and the creation of people-friendly workplaces
- Implementing organization formed from overlapping sub-groups down to the circle level, headed by the plant TPM Promotion Committee
- Activities implemented are individual improvement, self-led maintenance, planned maintenance, quality maintenance, initial product management, initial facility management, educational training, management and back office, and health and safety environment
- Activity content is evaluated with the indicators productivity (P), quality (Q), cost (C), delivery time (D), safety (S), environment (E), and morals (M)
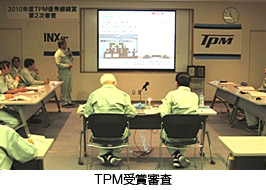
[Part II 1st Stage Activities]: 2005-2010 (TPM Ongoing Excellence Award received)
We developed activities with the goal to become the “No.1 Plant in Japan in the QCD Industry.”
- Priority issues are creative product development, innovative production methods, global human resource development, and people-friendly environments
- Activities are characterized by a full deployment of SAKATA INX’s unique through-neck analysis and taking an innovative approach to overcoming technical issues concerning the elimination of redundancy
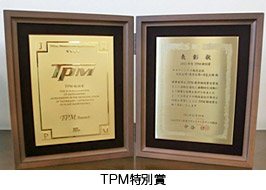
[Part II 2nd Stage Activities]: 2010-2012 (TPM Special Award received)
We developed activities with the goal to become the “No.1 Plant in Japan in the QCD Industry.”
- Priority issues are management system construction, achievement of innovative production methods, and development of global human resources
- The management system is formed of three foundations (enhancement of corporate character, propensity for improvement, maintenance structure) and two conditions (human resource development, analysis system), and we will construct a mechanism for permanent ongoing deployment
- In innovative production methods, we are constructing a system for maximum streamlining in manufacturing processes and centralized management of things and information with direct in/out
- In human resource development, we will train human resources capable of self-led management and turn them into human resources who can perform on the global stage
[Part III Activities]: 2013- Ongoing (2017 TPM Advanced Special Award received)
We developed activities with the goal to become the “3rd largest printing ink manufacturer in the world.”
- (1) Safe workplaces
Conduct a comprehensive review of latent risks in workplaces, work to mitigate risks that have become apparent, implement evaluation and management based on newly created indicators, and expand and enhance safety education - (2) Management system implementation
Put in place a system that permanently cycles through the three foundational aspects of corporate character enhancement, propensity for improvement enhancement, and maintenance structure enhancement - (3) Establishment and deployment of SDPS innovative production method
Using the through-neck analysis that characterizes SAKATA INX activities, we will clearly set out our goal, and establish and deploy the SAKATA INX Direct Production System (SDPS) that delivers maximum efficiency - (4) Human resource development
Develop the next generation human resources who are firmly committed to health and safety, capable of management anywhere in the world, and able to handle a turbulence-resistant production system. - (5) Overseas expansion and contribution to management
Support for and implementation of TPM activities with the goal of improving profit and contributing to management at increasingly important overseas facilities
[Results]
- Improvements in labor production, reduction in number of equipment malfunctions, reduction in number of claims, reduction in manufacturing lead times, prevention of accidents leaving to leave from work and accidents not leading to leave from work, reduction in CO2 equivalent emissions consumption rate, improvements in waste materials recycling rates
- In addition to 99% of all targeted employees obtaining qualifications as mechanical maintenance technicians and autonomous maintenance technicians, we have added human resources capable of building a flexible production system.
- We have increased visits to the plants of customers and companies pursuing TPM activities, and held regular plant tours for family members.
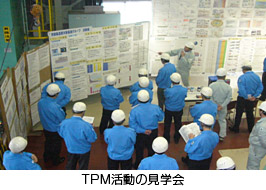
Overseas development
In order to promote TPM activities effectively, which has led to positive results in Japanese plants, at overseas locations, we began in 2005 by using Kansas Plant in North America as a model.
We implemented horizontal development of TPM activities at each main plant in North America from 2011, and have continued to develop activities also in the fast-growing Asia region.
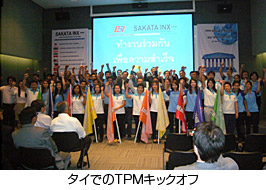
2005 | TPM activities launched at INX INTERNATIONAL INK CO.′s Kansas Plant.
(received TPM Excellence Award in 2010) |
---|---|
2011 | Implemented horizontal development of TPM activities at other main plants in INX INTERNATIONAL INK CO. |
2012 | TPM activities launched at the Maoming Plant in Guangdong, China. |
2013 | TPM activities launched in India, Indonesia, Thailand, Philippines, Malaysia and Vietnam. |
* The TPM trademark and logo are registered trademarks or trademarks of the Japan Institute of Plant Maintenance, both in Japan and in other countries.